Index
EffiBlech – CO2-effiziente elektrische Antriebe – Entwicklung einer industrietauglichen Prozesskette von gedruckten Magnetblechen (vom Pulver bis zum Bauteil)
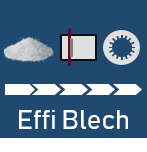
In elektrischen Antrieben entstehen bei der Energiewandlung Verluste, die zu einer Erwärmung der Maschine führen und abgeführt werden müssen. Zu den Gesamtverlusten tragen maßgeblich die Eisenverluste bei, die durch den Einsatz von Fe-Si-Elektroblechen reduziert werden können. Gängige Elektrobleche werden in aufwendigen mehrstufigen Umform- und Wärmebehandlungsprozessen hergestellt und anschließend zu Rotor- bzw. Statorblechpaketen verarbeitet. Bedingt durch die Prozessschritte Walzen und Stanzen ist die zu verarbeitende Minimaldicke der Bleche begrenzt und liegt standardmäßig zwischen 0,2 und 0,65 mm, weshalb eine weitere Reduzierung der Wirbelstromverluste nicht möglich ist. Weiterhin fallen bei der Formgebung der Elektroblechlamellen Materialverschnitte von bis zu 50 % an, so dass ein Großteil des unbenutzten teuren Materials erneut aufbereitet werden muss.
Das Forschungsprojekt EffiBlech wird im Rahmen des 7. Energieforschungsprogramms des Bundesministeriums für Wirtschaft und Energie (BMWi) gefördert und im Verbund mit industriellen sowie wissenschaftlichen Partnern durchgeführt. Der Lehrstuhl FAPS beteiligt sich in diesem Projekt in den kommenden drei Jahren mit der Erforschung von Produktions- und Prüfverfahren für eine pulvermetallurgisch-drucktechnische Herstellungsroute von dünnen Elektroblechen.
Die Firma Siemens fungiert als Projektkoordinator und ist sowohl bei der Erforschung der Pasten und des Druckprozesses als auch bei der Weiterverarbeitung und Prüfung der Bleche im Projekt beteiligt. Das Fraunhofer IFAM ist maßgeblich für die Pastenentwicklung und den Herstellungsprozess der Einzelbleche zuständig, wobei die Firma EKRA die Fertigungsanlage für den Druckprozess entwickelt. Ein wichtiger Verarbeitungsschritt ist die Wärmebehandlung der Bleche, weshalb sich die Firma MUT mit der produktspezifischen Entwicklung des Wärmebehandlungsprozesses im Rahmen des Projektes beschäftigt. Zur Gewährleistung der Bauteilqualität ist die Firma Optonic für die Integration geeigneter Inspektionssysteme zuständig. Die Arbeitspakete des Lehrstuhls FAPS fokussieren sich einerseits auf die Weiterverarbeitung der gedruckten Bleche und andererseits auf die Optimierung der Gesamtprozesskette. Ein Schwerpunkt liegt in der Erforschung potentieller Isolationssysteme sowie dessen Applikation, damit eine elektrische Trennung zwischen den Blechen sichergestellt wird und die Wirbelstromverluste minimiert werden. Weiterhin muss ein Konzept für die industrielle Einführung entwickelt und der Primärenergiebedarf des neuartigen Herstellungsprozesses analysiert und optimiert werden.
OptiWiRE – Optimierte Wickel- und Montageverfahren für recyclinggerechte Elektromotoren
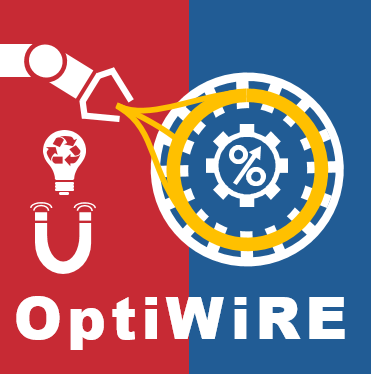
Die Ziele des Vorhabens OptiWiRE, mit den Verbundpartnern ElringKlinger AG und dem Lehrstuhl FAPS, sind eine Verbesserung der Prozesskette bei der Herstellung von Elektromotoren, in Bezug auf der in der Automobilbranche sehr hohen Anforderungen an Taktzeit, Qualität und Flexibilität der Fertigung. Ein wesentliches Ziel, zu dem dieses Projekt beitragen soll, ist die Übergang von der Prototypen-Fertigung zur Vorserienproduktion. Weiter zielt das Vorhaben auf eine Effizienzsteigerung der Elektromotoren ab um eine höhere Lebensdauer der Motoren zu erreichen und um auch den Energieverbrauch von E-Fahrzeugen und die damit verbundene Reichweite zu erhöhen. Hinsichtlich der Leistungsfähigkeit kritische Fertigungsprozessschritten wurden bereits in Voruntersuchungen identifiziert. Dabei konnten wesentliche Optimierungspotentiale bei der Wicklungsherstellung am Stator und bei der Magnetmontage im Rotor festgestellt werden. Für diese beiden Prozessschritte sollen im Rahmen des Projektes Verbesserungen hinsichtlich des Produktes E-Maschine und der Produktion durch die Adaption neuer Verfahren erzielt werden.
Innerhalb des Gesamtvorhabens OptiWiRE wird im Teilvorhaben “füllgradoptimierte, automatisierte Statormontage von verteilten Einzugswicklungen” vom Lehrstuhl FAPS der FAU die Prozesskette der Statorproduktion ausgehend vom Statorblechpaket bis zur Kontaktierung der Stern- und Phasenverbinder betrachtet. Auf Grund von höheren Automatisierungspotentialen soll im Bereich der Stator-Fertigung das Einziehwickelverfahren für den industriellen Einsatz mit dem Ziel weiterentwickelt werden, flexibel auf Varianten- und Stückzahländerungen reagieren zu können. Ein wesentlicher Ansatz ist es dabei, den Draht definierter abzulegen, um den Kupferfüllgrad im Stator zu erhöhen sowie die Taktzeit des Prozesses zu verringern. Dies soll durch die flexible Automatisierung der dem Wickeln vor- und nachgelagerten Prozesse realisiert werden. So sollen insbesondere bei der Handhabung und Prozessführung von losen Leiterenden und Drahtbündeln deutliche Verbesserungen erreicht werden, um höchste Qualität und kürzeste Taktzeiten bei steigenden Produktionsmengen realisieren zu können.
Im Teilvorhaben “Prozessentwicklung beim Rotorbau – Fixierung der Magnete” untersucht die ElringKlinger AG die Optimierung der Rotorbaugruppe des im Projekt verwendeten Elektromotors. Das Verkleben der Magnete stellt den Stand der Technik im Bereich der Magnetmontage dar. Dies hat den Umgang mit Chemikalien, langen Prozesszeiten und aufwendigen Temperiervorgängen zur Folge. Durch die stoffschlüssige Verbindung von Magnet, Klebstoff und Rotorpaket lassen sich diese Komponenten nach der Lebensdauer des Motors im Recyclingprozess kaum noch voneinander trennen. Beim Versuch die Seltenen-Erde-Magnete aus dem Rotorpaket zu lösen zerbrechen diese. Eine sortenreine Trennung von Magneten und Blechmaterial ist ebenfalls durch die stoffschlüssige Verbindung des Klebstoffes erschwert. Rückstände des Klebstoffes bleiben an den Bauteilen haften. Diesen Herausforderungen stellt sich die ElringKlinger AG durch Entwicklungen von innovativen Magnetfixierungsstrategien.
transform_EMN: Transformation of the automotive and supplier industry in the Nuremberg Metropolitan Region
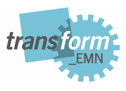
Around 100,000 employees in the Nuremberg Metropolitan Region work for suppliers of the automotive industry. Many of the jobs depend on the combustion engine and are endangered by the transformation of the industry. The large-scale project transform_EMN with a volume of 6.6 million euros supports companies, among other things, in the development of new business ideas and technology transfer.
The FAPS is responsible for setting up and operating the innovation platform “Transformation-oriented Production – Sustainable and Digital Manufacturing”. Participating SMEs from the automotive and supplier industry are given the opportunity to test technologies for digital, energy-efficient and climate-friendly production, to develop these further together with scientists from the participating research institution, and to demonstrate the production capabilities gained. Based on these experiences, the chair develops and disseminates a variety of qualification offers and consulting measures.
In the context of the digitalization of production, the chair is developing needs-based solutions for the local supplier industry. In order to achieve a cost-efficient and low-threshold entry, the use of open-source software and modern cloud technologies is to be promoted in particular. The focus will be on the derivation of suitable data models, the investigation of state-of-the-art communication technologies and the demonstration of artificial intelligence methods. In the context of systematic intelligence enhancement, the knowledge gained will be demonstrated in practice on innovative production systems.
The second in-depth topic is the conversion to sustainable and CO2-neutral production. The design of sustainable and intelligent energy distribution architectures for production sites as well as the integration of decentralized, regenerative generators and storage systems both from a hardware perspective and the intelligent coupling and transfer to an “Industrie 4.0”-compliant energy management play an essential role here. Efficient direct current grids should be mentioned as a special solution concept.
MuViS – Hybrid AI for adaptive, data-efficient, and explainable multi-view visual inspection of multi-variant assemblies
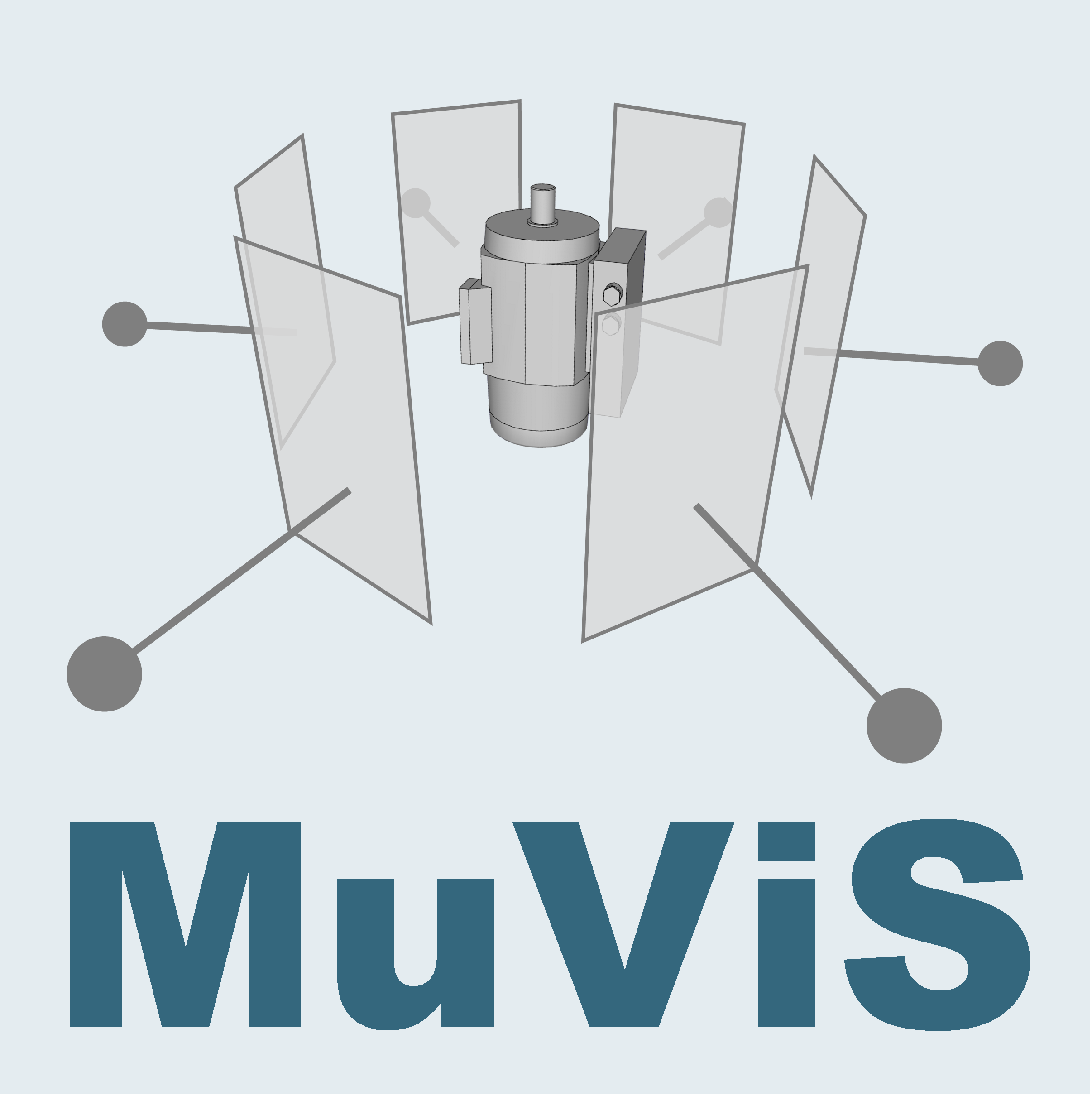
Although the range of applications for image processing has been growing for years, only a portion of industrial visual inspection tasks have been automated to date. Artificial intelligence (AI) methods hold the potential to automate even difficult visual inspection tasks that have been performed manually so far. Since classical deep learning (DL) techniques require a large amount of training data, they are hardly applicable for inspection objects with high variance and small batch sizes. Furthermore, common DL architectures are typically restricted to the evaluation of single image perspectives, have limited explanatory power due to their inherent black-box nature, and lack the ability to incorporate existing factual and rule knowledge. Accordingly, the goal of the present research project is to meet the aforementioned challenges by developing a hybrid, data-efficient AI solution, making it possible to automatically inspect assembly assemblies with a high number of variants in the near future.
ProKI-Nürnberg – Demonstration and transfer center for applying artificial intelligence in joining technology as part of the nationwide ProKI network
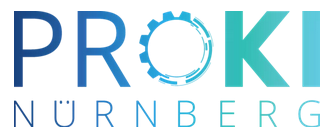
ProKI-Nürnberg is one of eight ProKI centers of the ProKI network in Germany. The ProKI network serves companies, especially SMEs, as a central hub for training and consultancy on using artificial intelligence (AI) in production. The focus of the ProKI center in Nuremberg lies on AI use cases in joining technology, especially in the field of electronics production and electromechanical engineering.
Further information on current events and contacts can be found on: www.proki-nuernberg.de
REEPRODUCE – Recycling of permanent magnets from end-of-life products

Rising prices and supply insecurities of industrial raw materials are threats to the production of innovative products and thus the climate goals of the European Union. Hard to replace rare earth elements (REE), which e.g. are used in the production of semiconductors or permanent magnets and therefore also electric motors, are of a particularly great significance. These REEs are mainly imported from the PR China, which, looking at the export restrictions of the present and past, imposes great risks to the supply security of the European industry. The reduction of import dependency in the field of rare earths, for example by creating an intra-European recycling circuit, is therefore in the great interest of the European Union. Research projects have already shown that a closed recycling process in the field of rare earth-based permanent magnets is feasible in principle.
Within the framework of the EU-funded research project REEPRODUCE, 15 research and technology institutions from eight European countries, with the participation of the FAPS, are to enable the economic separation of hard magnetic components starting from various end-of-life (EoL) products. The €10.1 million Horizon Europe program-funded project, led by SINTEF (Norway), will continue to demonstrate the viability of recycling techniques on an industrial scale and investigate the environmental impact of recycling REEs. This will cover the entire value chain starting from EoL products to the production of new permanent magnets. The project contributes to achieving the EU’s ambitious climate targets by 2030, while strengthening the competitiveness of the European industrial raw materials sector.
ProDRIMo – Flexible assembly of limp wire and insulation materials by AI-based robotic systems in the production of electrical machines
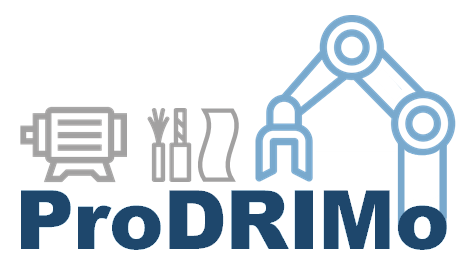
Using advanced sensors, actuators and methods of artificial intelligence (AI), robots are increasingly turning into learning systems that interact with humans, make decisions and take on more complex tasks. As a result, new application potentials are opening up that go beyond the classic application areas of industrial robots. Especially the production of electrical machines, whether electric motors, generators or transformers, is still characterized by manual assembly operations due to limp materials and components. Due to the high wage level in Germany, processes that require the handling of limp insulation and wire materials are increasingly being relocated to foreign countries. This trend is particularly noticeable among medium-sized manufactures, who generate a large part of their sales from the production of customized electrical machines in small to medium quantities. Therefore, the aim of the ProDRIMo research project is to explore innovative system solutions for robot-based assembly of limp insulation and wire materials, contributing to the automation of previously manual processes in the manufacture of electrical machines. The key technological enablers are novel tactile and optical sensors, high-performance hardware, mechatronic end effectors, and AI-based methods for perception and control. On behalf of all manufacturers of electrical machines, the researched system modules are being tested on the basis of two concrete application examples. In the long term, the developed solutions can also be transferred to other areas of the electrical industry.
ExApeMo – Expert system for the analysis of permanently excited motors
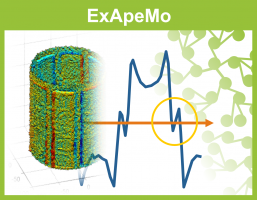
The current development of electric drives not only focuses on reducing manufacturing and failure costs but also on increasing efficiency and power density. The latter is mainly achieved by the use of permanently excited machines since these machines operate without the electrical generation of the rotor magnetic field due to their design. This eliminates ohmic losses, which potentially means higher efficiency. The air gap field, which is built up by the rotor and stator, has a considerable influence on the quality of a permanently excited synchronous motor. However, the effects of the magnetic fields on the essential target values of a drive with regard to optimum power density, reduction of cogging torques, avoidance of vibrations, and reduction of noise emissions can only be considered to a limited extent in the manufacturing process.
Already existing measuring systems for the characterization of magnetic components allow the testing of the magnetic stray field within the scope of development processes. However, the use of these measuring devices requires special expertise in the field of electrical engineering and the evaluation of the measurement results calls for in-depth knowledge in the field of motor design. Moreover, the measurement and evaluation tools do not offer the possibility to import geometry descriptions and simulation data and to include them in the interpretation of the collected measurement data.
Within the project ExApeMo missing technical links between magnetic field simulation and magnetic field measurement of permanently excited motors will be developed and a software for the integration of measurement data and the identification of deviation causes will be conceptualized and prototypically realized.
KIKoSA – Artificial intelligence for reliable laser-based contacting of stators for electric drives
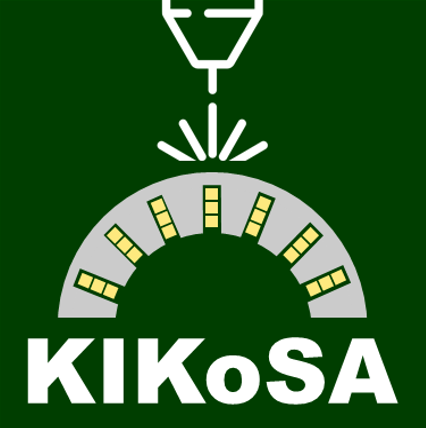
In the course of series production of automotive traction drives, stators in hairpin technology are increasingly coming into focus. Due to the high number of contact points, the laser-based contacting of wire ends plays a major role in hairpin stator production. To realize a stable laser welding process, on the one hand, all influencing variables within the laser welding process itself must be known. On the other hand, relevant interactions with upstream process steps that may have a negative effect on the welding result must be taken into account. Since hairpin stator production is thus characterized by a superposition of numerous non-linear effects, classical methods are reaching their limits when it comes to mapping the causal relationships. Furthermore, there is no fast, cost-effective test method that allows an inline monitoring of the quality of each welded joint, such as the size and number of pores.
In this context, data-driven approaches using the methods of artificial intelligence (AI) are becoming increasingly interesting. Therefore, the project KIKoSA investigates to what extent the quality of welded joints can be monitored using AI based on available material and process data as well as easily integrable sensors. The desired AI solution should enable the detection of deviations in upstream process steps at an early stage and their compensation by an intelligent adaptation of the laser welding process. In this way, this project makes a significant contribution to increasing efficiency in the production of electric drives for electric vehicles.
E|KI-Opt – Explainable artificial intelligence for the holistic optimization of processes in electric motor production
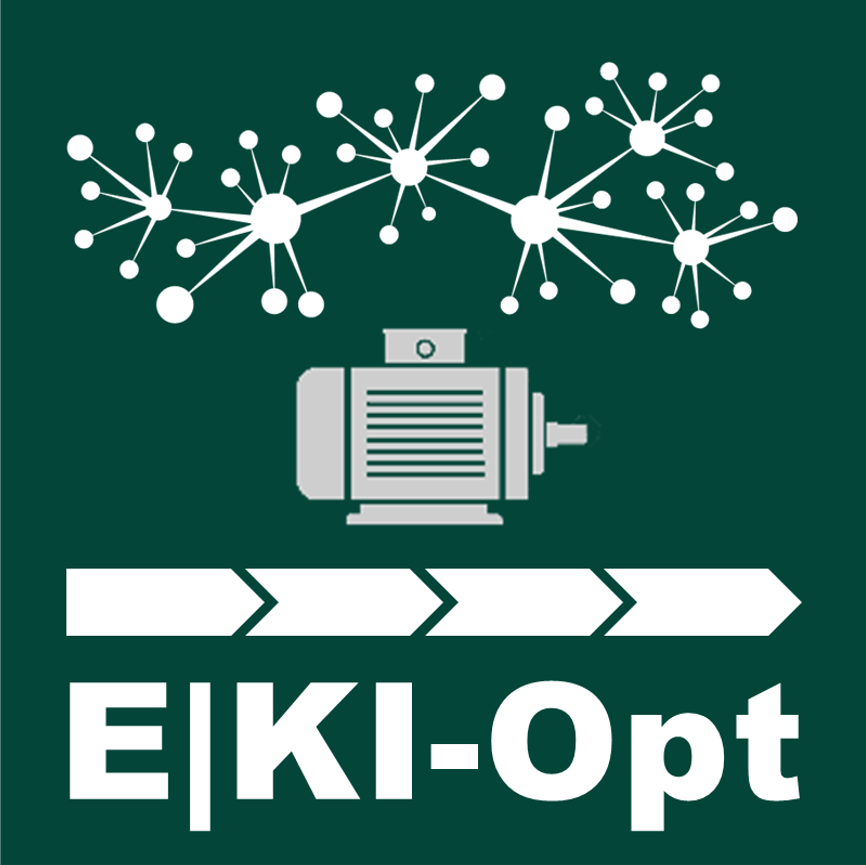
Industry 4.0 is accompanied by a variety of technologies that offer great potential for tomorrow’s electric motor production. In particular, data-driven approaches applying methods of artificial intelligence (AI) are increasingly coming into focus. So far, however, only a few scientific works have dealt with the potential of data-driven approaches in electric motor production. As a result, there is a lack of industry-specific best practices that electric motor manufacturers could use for orientation. Another reason for the hesitant adaptation of AI methods is the black-box character of the widely propagated deep learning algorithms as well as the often missing opportunity to integrate existing domain knowledge.
Therefore, the aim of the project E|KI-Opt is to exploit the potential of AI for process and production optimization in electric motor manufacturing by using data-driven approaches that are as explainable as possible as well as to derive best practices for the entire industry. On the one hand, cross-process relationships are to be detected and an AI model for predicting the electric motor’s quality based on material, process, and test data is to be derived. On the other hand, essential, quality-relevant sub-processes are to be optimized using AI as well. Building on the domain expertise of the participating plant manufacturer and operator as well as the AI expertise of the IT service provider and university, E|KI-Opt aims to create explainable and robust AI solutions that improve the production of electric motors and enrich the industry players with new AI-based business concepts.